Optimizing Valve Sealing
Optimized for high wear resistance and low friction combined with high tightness, for high temperature applications.
Conventional valves may have stuffing box chambers with 7 and more rings. Current knowledge, based on modern packing material, recommends the use of a maximum of 4-6 packing rings. The remaining space should be filled for example with a pressure resistant carbon bushing. These bushings are usually split in 2 halves to simplify installation. Other materials, resistant to temperature and pressure, can be used as well. The idea behind this measure is to equalize the available gland force between the packing rings.
A reduction from 7 to 5 packing rings can lower the necessary gland force of a rough packing with a low K value to less than half. This reduces as well the risk of extrusion of packing material between gland and stem, and still delivers the same compression at the bottom ring.
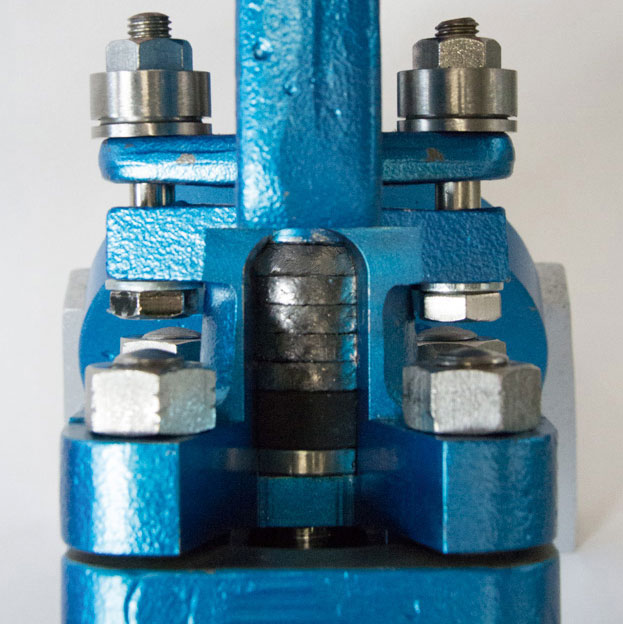
Optimized valve sealing with Carbon bushing, wiper ring and bullring.
1. Reduction
Carbon bushing for reduction of stuffingbox depth
Carbon bushing can be used to reduce the gland forces, which are necessary to compress a packing stack to seal at the stuffingbox bottom.
The bushing can be supplied split or un-split.
Type | Density | Compressive strength | Temperature resistance in atmosphere | inert |
---|---|---|---|---|
PP4 | 1.7 | 100 N/mm2 | 500 °C | 2500 °C |
PP32 | 2.5 | 290 N/mm2 | 500 °C | 550 °C |
PP89 | 1.75 | 120 N/mm2 | 500 °C | 2500 °C |
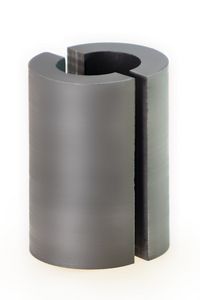
Optimized valve sealing with Carbon bushing
Axial compression to sealing force conversion (K value)
Blue = 0,75 Carbon Yarn Packing (A33)
Red = 0,80 eGraphite/graphite fiber packing (A22, A44I, A66)
Magenta = 0.88 eGraphite and PTFE packing (A19, A19OX, A37, A99, TP55)
2. Extrusion
3. Prepress
4. Live Loading
Using ProPack LiveLoadingSystem enables faster maintenance. You can see a detailed description under the menu item "LiveLoading".